時計について6
方向幕の項でも触れていますが、私は「はんだ」作業が大の苦手です。
右手で柄の長いコテを持ち、左手ではんだを供給する場合、肝心の基盤は誰も持っていないことになります。
さらに、極小の溶接面に対してコテのグリップは溶接点からあまりに遠く、精密作業に不向きな道具構造なのは明らかだと思います。
加えて、手早く行うのが鉄則とされる作業も、私の安価なはんだコテでは温度が一定しないのか、いくら基盤にコテ先を押しつけてもはんだは溶解せず、基盤の表面が焦げるか、周辺に高温が伝わって私がアセるか、不意に不細工に溶けたはんだが固まって「イモはんだ」を連発するか、再び除去しても松脂が汚く残るか、のどれかです。
さすがにはんだ作業の基本を検索してみると、初心者には温度調節式のコテが良いと判り、後に5,000円もするタイプを購入してしまいますが、それでもあまり成果はありませんでした。
話が脱線しましたが、この時の作業は例外的に、概ね2/3の確率で良いはんだとされる「山」型を作ることができました。
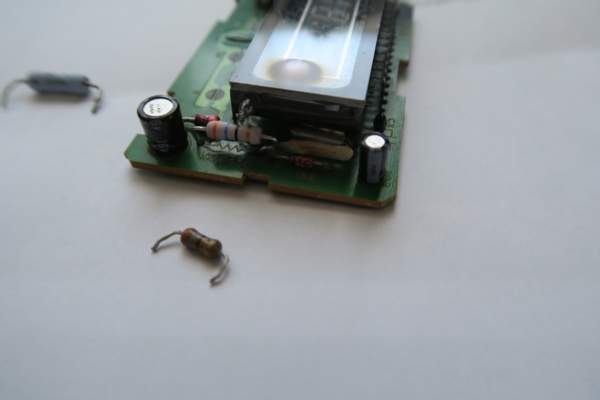
■交換した36Ω。脚を長めにカットし、基盤面から少し浮かせる形で実装。
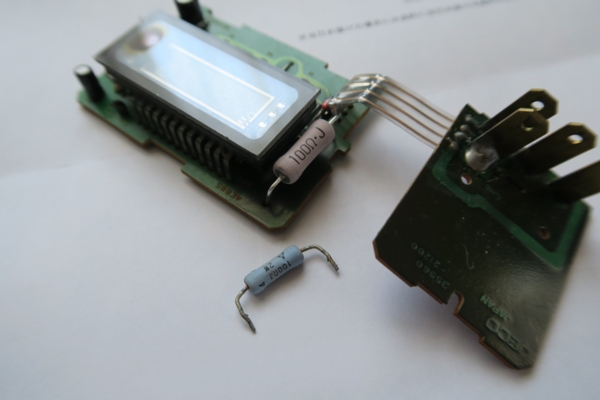
■交換した100Ω。リード穴に片側が収まらないので、片脚を内側に折り曲げる形とし、浮かせて実装。
蛍光表示管からなるべく離すため、やや傾斜も付けた。
そこで早速電源を繋いで、様子をみてみます。
すると、換装前と同様に見事に点いてくれましたので、素人としては喜ばしい限りです。
しかし2個の抵抗のうち、36Ω側は温度も上昇せず換装に成功したのですが、100Ωの方は以前と同様に高熱を発し、換装の効果はみられませんでした。
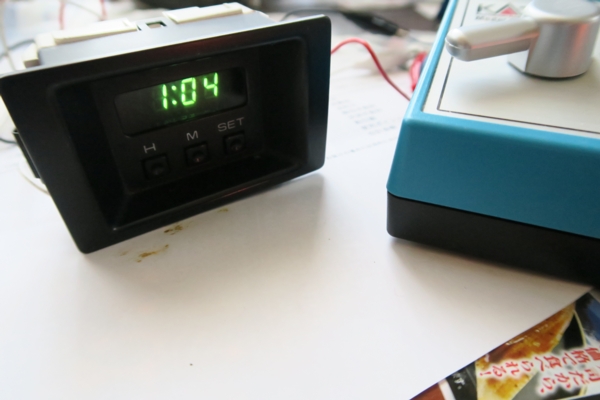
■ケースに入れて再度実験。
ならば、とケースがヒートシンクのような役割をして熱を外に逃がすのではないかと思い、基盤をケースに収めて実験してみましたが、ケースの外側は熱くなってきたものの放熱効果は低いようで、30分ほどで中止しました。
ここでケースを開けてみますと、中にはすごい熱気がこもっています。
これでは蛍光表示管や電解コンデンサへの悪影響が大きすぎるので、何らかの改造が必要に思いました・・・。